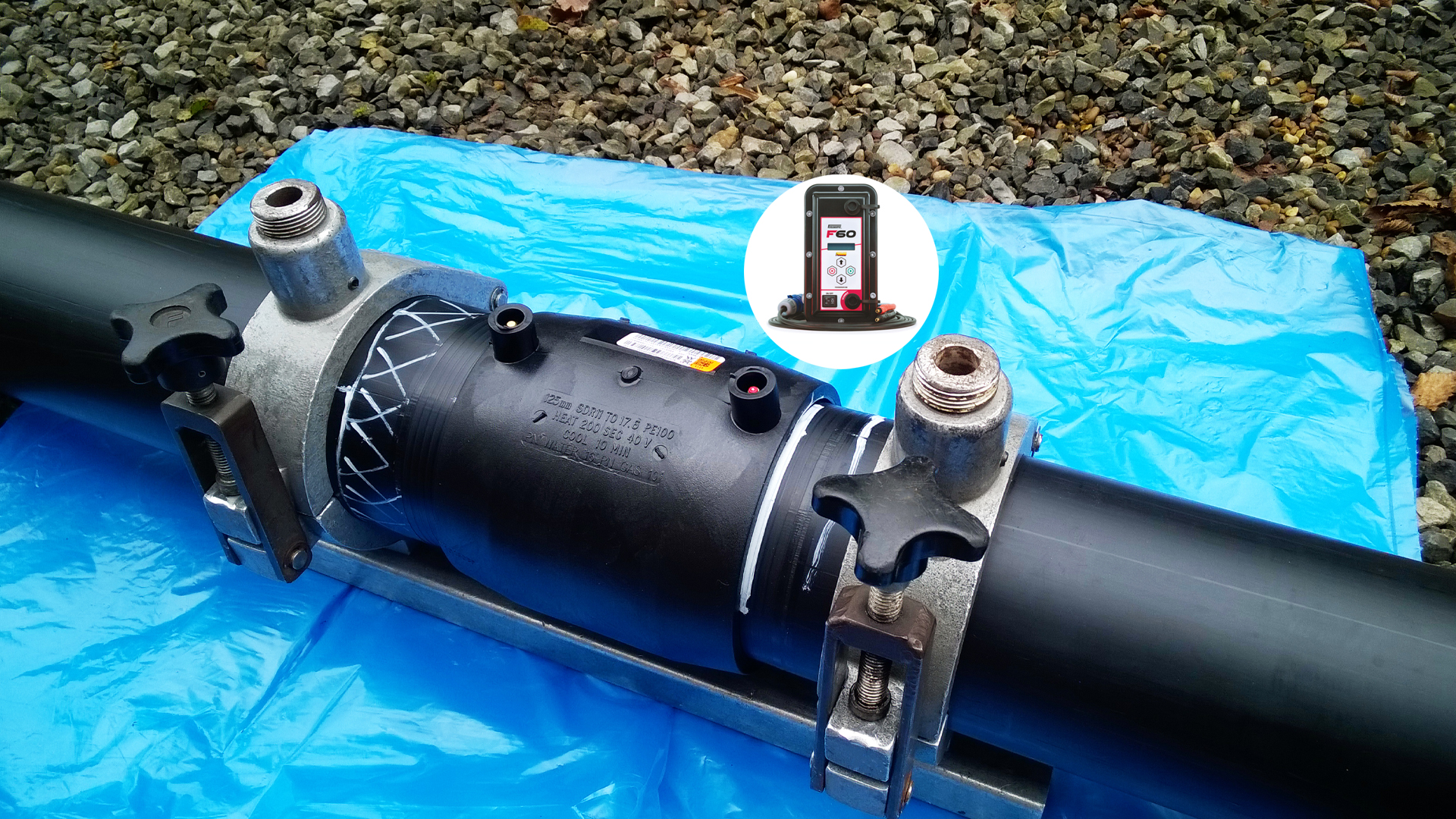
PE-Elektroschweißen von Rohren und Fittings
Der Einsatz von Kunststoffprodukten aus Polyethylen (PE) im Bau von Verteilungs- und Versorgungsleitungen für Gas und Wasser liegt voll im Trend. Den vielen Vorteilen von PE-Rohren und Fittings, vor allem das niedrige Gewicht, lange Lieferlängen und große Flexibilität der Rohre oder die lange Nutzungsdauer, stehen nur relativ wenige Nachteile wie beispielsweise Empfindlichkeiten gegen mechanische Belastung oder gegen UV-Einstrahlung entgegen. Ein großer Vorteil ist auch die einfache und sichere Schweißbarkeit zur Herstellung von zuverlässigen Verbindungen. 13-02-2025
Zur Herstellung der Elektroschweißverbindung von PE-Rohren und PE-Fittings sind wichtige Parameter zu beachten, die sich aus den Materialeigenschaften ergeben. Einfluss auf das Ergebnis haben Temperatur und Zeitdauer des Schweißvorgangs, beim Stumpfschweißen zusätzlich der axiale Druck. Der Erfolg des Schweißvorgangs hängt außerdem sehr von den sorgfältigen Vorarbeiten ab, wobei die Sauberkeit und die Fettfreiheit der Flächen, der Werkzeuge und der benutzten Heizelemente von großer Bedeutung sind. Deswegen ist die Verwendung von Reinigungsmitteln angesagt, die zu 100 Prozent verdampfen.
Werfen wir einen Blick auf die gängigen Verfahren Heizelementstumpfschweißen und Heizwendelschweißen. Für beide Verfahren werden spezielle Geräte und Maschinen benötigt, um zwei Rohre beziehungsweise Komponenten erfolgreich miteinander verbinden zu können. Ein großer Unterschied ist, dass beim Heizwendelschweißen zusätzliche PE-Formteile wie Elektroscheißmuffen eingesetzt werden, die damit ein fester Bestandteil des PE-Rohrnetzes werden. Im Gegensatz dazu wird beim Heizelementstumpfschweißen kein zusätzliches Teil benötigt. Rohre und möglicherweise Armaturen werden direkt miteinander verbunden.
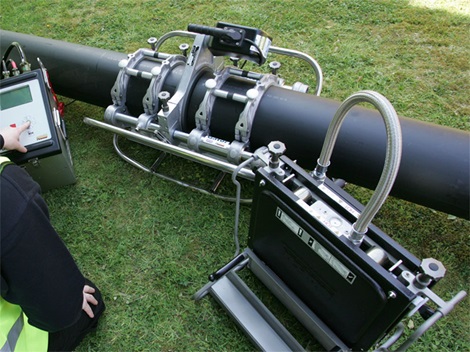
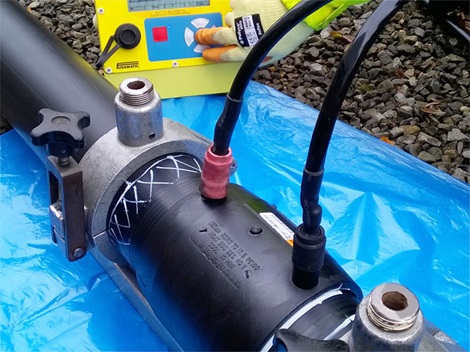
Beim Heizelementstumpfschweißen (linkes Bild) werden zunächst die beiden zu verbindenden Teile axial exakt ausgerichtet. Ein Versatz sollte dabei vermieden beziehungsweise auf ein Minimum begrenzt werden. Eine Montagevorrichtung hilft, die Teile gegeneinander zu drücken und die Schweißflächen anzugleichen. Ein Heizelement zwischen den Teilen wird dann auf Schweißtemperatur erhitzt. Haben die beiden Rohrenden diese erreicht, wird das Heizelement entfernt und die Teile werden mit vorgegebenem Druck gegeneinander gepresst. Anschließend folgt die Abkühlphase. Während des Schweißens und Abkühlens sollte die Schweißstelle nicht mechanisch belastet werden. Die benötigte Arbeitszeit des gesamten Vorgangs teilt sich auf in 90 Prozent Vorbereitung, 4 Prozent Schweißzeit und 6 Prozent Abkühlphase. Dazu kommt die nötige Nachbearbeitungszeit für das Entfernen des beim Schweißen entstehenden Wulstes im Rohr, was bei Rohrlängen von 6 Metern aufwändig sein kann.
Für das Heizwendelschweißen (rechtes Bild) empfehlen sich automatische Schweißgeräte, die die richtigen Werte für Zeiten und Temperatur mittels Scanner einlesen. Eine besonders komfortable Lösung sind Elektroschweißfittings und Geräte wie unsere AVK Fusamatic Produkte: Mittels des automatischen Fusamatic Stifts können AVK Schweißgeräte wie F60 oder F90 die korrekten Schweißparameter vollkommen automatisch erfassen. Auch bei diesem Schweißverfahren hängt viel von der perfekten Vorbereitung ab: So müssen die Schweißflächen senkrecht aufeinander ausgerichtet werden. Schweißbereich und Schweißmuffe müssen von Oxid befreit und sauber und fettfrei sein. Der Einsteckbereich wird ausgemessen und markiert, um sicherzustellen, dass das Rohr weit genug in die Muffe eingeführt wird. Nach dem Zusammenfügen der Komponenten werden die elektrischen Anschlüsse hergestellt, die Scheißparameter mittels Scanner oder automatisch erfasst und der Scheißvorgang gestartet. Ein erfolgreicher Scheißvorgang wird optisch durch einen aufsteigenden Pin an der Scheißmuffe signalisiert. Nach der Abkühlphase ist auch dieser Scheißvorgang abgeschlossen. Bei AVK Fusamatic Produkten entfällt übrigens die sekundäre Abkühlzeit.